Production Capacity Calculator
The production capacity calculator helps you calculate how many pieces of your product you will be able to make in a day.
Enter the total number of machines, shift hours per day, product SAM, and line efficiency to calculate the production capacity.
When you click the calculate button, you will be able to see the production capacity as the number of pieces that your unit or factory can make.
In case you don’t know, production capacity refers to how many products a company can make in a certain amount of time. This indicator helps a company make important short-term and long-term business decisions.
The formula to calculate the production capacity is:
Production capacity (in pieces) = (Capacity in hours X 60/product SAM) X line efficiency
Where:
Product SAM = How long it takes to produce one unit of product
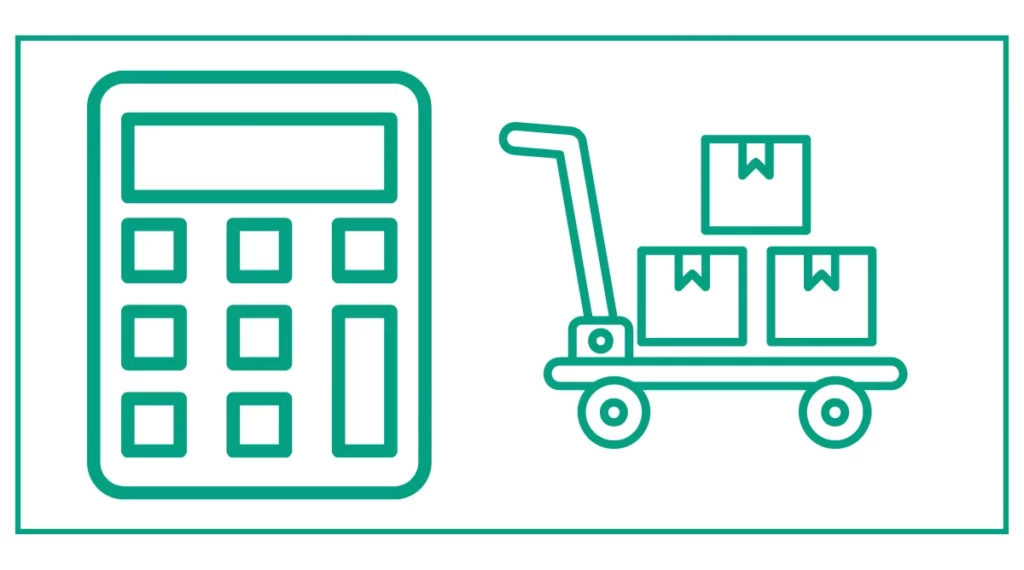
You might also want to find out the lead time or the value of your business website.
What is Production Capacity?
Production capacity is the maximum potential output of a manufacturing process or production line within a specific timeframe. It takes into account factors such as available resources, working hours, and efficiency rates. Knowing your production capacity allows you to:
- Plan production schedules effectively
- Allocate resources efficiently
- Identify bottlenecks in the production process
- Make informed decisions about expansion or scaling
Why Calculate Production Capacity?
Calculating production capacity is crucial for several reasons:
- Optimize Resource Allocation: By understanding your maximum output, you can better allocate resources and avoid overstaffing or underutilization of equipment.
- Improve Production Planning: Accurate capacity calculations help in creating realistic production schedules and meeting customer demand.
- Identify Bottlenecks: Capacity analysis can reveal production bottlenecks, allowing you to address issues and improve overall efficiency.
- Make Informed Decisions: Knowledge of your production capacity aids in decision-making regarding expansion, new product lines, or accepting large orders.
How to Calculate Production Capacity
Calculating production capacity involves several steps and considerations. Here’s a step-by-step guide to help you determine your manufacturing facility’s output potential.
Step 1: Determine Available Production Time
First, calculate the total available production time:
- Identify the number of working days per year
- Determine the number of shifts per day
- Calculate the number of working hours per shift
- Account for planned downtime (maintenance, holidays, etc.)
Example:
- 250 working days per year
- 2 shifts per day
- 8 hours per shift
- 10% planned downtime
Available production time = 250 * 2 * 8 * 0.9 = 3,600 hours per year
Step 2: Assess Equipment Capacity
Next, evaluate the capacity of your production equipment:
- Identify the number of machines or workstations
- Determine the output rate for each machine (units per hour)
- Consider any equipment-specific constraints or limitations
Example:
- 10 machines
- Each machine produces 50 units per hour
Theoretical equipment capacity = 10 * 50 = 500 units per hour
Step 3: Factor in Efficiency and Utilization Rates
To get a more realistic picture, incorporate efficiency and utilization rates:
- Determine the overall equipment effectiveness (OEE)
- Consider labor efficiency and skill levels
- Account for material availability and quality
Example:
- OEE of 85%
- Labor efficiency of 90%
Adjusted capacity = 500 * 0.85 * 0.9 = 382.5 units per hour
Step 4: Calculate Daily and Annual Production Capacity
Using the information from previous steps, calculate your daily and annual production capacity:
Daily production capacity = Adjusted capacity * Working hours per day
Annual production capacity = Daily production capacity * Working days per year
Example:
Daily production capacity = 382.5 * 16 = 6,120 units per day
Annual production capacity = 6,120 * 250 = 1,530,000 units per year
Using the Production Capacity Calculator
To simplify the process of calculating production capacity, we’ve provided a user-friendly calculator tool. This capacity calculator takes into account key factors to determine your manufacturing facility’s output potential.
How to Use the Calculator
- Enter the total number of machines in your production line
- Input the number of shift hours per day
- Provide the Standard Allowed Minutes (SAM) for your product
- Enter your line efficiency percentage
- Click “Calculate” to get your production capacity result
The calculator will process this information and display your daily production capacity in pieces.
Interpreting the Results
The result shows the number of units your production line can produce in a day under the given conditions. This information can be used to:
- Set realistic production targets
- Identify areas for improvement in efficiency
- Make decisions about accepting orders or expanding capacity
Remember that this calculation provides a theoretical maximum. Real-world factors may affect actual output, so it’s essential to monitor and adjust your production planning accordingly.
Maximizing Production Capacity
Once you’ve calculated your production capacity, the next step is to look for ways to maximize it. Here are some strategies to increase your production capacity and improve overall efficiency:
1. Implement Lean Manufacturing Principles
Adopting lean manufacturing principles can significantly improve your production capacity by reducing waste and optimizing processes. Key concepts include:
- Value stream mapping to identify and eliminate non-value-adding activities
- Just-in-time production to reduce inventory and improve flow
- Continuous improvement (Kaizen) to constantly refine processes
2. Optimize Workflow and Layout
Improving your production facility’s layout and workflow can lead to increased capacity:
- Analyze and optimize material flow
- Reduce unnecessary movement of people and materials
- Implement cellular manufacturing where appropriate
3. Invest in Technology and Automation
Upgrading equipment and implementing automation can boost production capacity:
- Invest in more efficient machinery
- Implement robotics for repetitive tasks
- Use production management software for better planning and control
4. Enhance Worker Skills and Productivity
Your workforce plays a crucial role in maximizing production capacity:
- Provide regular training to improve skills and efficiency
- Implement ergonomic workstations to reduce fatigue and increase productivity
- Encourage employee involvement in process improvement initiatives
5. Manage Bottlenecks
Identifying and addressing bottlenecks in your production process can significantly increase capacity:
- Use capacity planning tools to identify constraints
- Implement the Theory of Constraints to focus on system-wide improvement
- Consider adding resources or redistributing work to alleviate bottlenecks
6. Improve Quality Control
Enhancing quality control measures can indirectly increase production capacity:
- Implement statistical process control to reduce defects
- Use preventive maintenance to reduce equipment downtime
- Improve supplier quality to reduce material-related issues
Production Capacity Planning: Looking Ahead
Effective production capacity planning is crucial for long-term success. Here are some key considerations:
1. Forecast Demand
Accurate demand forecasting is essential for capacity planning:
- Analyze historical data and market trends
- Collaborate with sales and marketing teams for insights
- Consider seasonal fluctuations and industry cycles
2. Evaluate Capacity Utilization
Regularly assess your capacity utilization rate:
- Calculate the ratio of actual output to potential output
- Identify periods of under or over-utilization
- Make informed decisions about scaling production
3. Plan for Growth
Anticipate future capacity needs:
- Consider long-term business goals and market projections
- Plan for gradual capacity increases to meet growing demand
- Evaluate options for expansion or outsourcing
4. Balance Flexibility and Efficiency
Strive for a balance between efficiency and adaptability:
- Consider implementing flexible manufacturing systems
- Maintain some excess capacity to handle demand fluctuations
- Evaluate the trade-offs between specialization and versatility
Frequently Asked Questions
How often should I calculate my production capacity?
A: It’s advisable to review your production capacity regularly, at least quarterly. However, recalculate more frequently if there are significant changes in your production process, equipment, or workforce.
Can production capacity change over time?
Yes, production capacity can change due to various factors such as equipment upgrades, process improvements, changes in workforce skill levels, or shifts in product mix.
How does capacity utilization relate to production capacity?
Capacity utilization is the ratio of actual output to potential output (production capacity). It indicates how effectively you’re using your available resources and can highlight opportunities for improvement.
What’s the difference between theoretical and actual production capacity?
Theoretical capacity is the maximum possible output under ideal conditions. Actual capacity takes into account real-world factors like downtime, inefficiencies, and variability in processes.
How can I increase my production capacity without major investments?
Focus on optimizing existing processes through lean manufacturing principles, improving workflow, enhancing worker skills, and addressing bottlenecks. These methods can often yield significant improvements without large capital expenditures.
In conclusion, understanding and optimizing your production capacity is crucial for manufacturing success. By using tools like the production capacity calculator and implementing strategies to maximize output, you can improve efficiency, meet customer demand more effectively, and position your business for sustainable growth. Regular assessment and thoughtful planning will ensure that your production capacity aligns with your business goals and market demands.
References
- Tursunov, B. O. “Principles and functions of management of production capacity.” Вопросы управления 3 (46) (2017): 174-178.
- How to Calculate Production Capacity of a Factory? (2018, September 10). Online Clothing Study. onlineclothingstudy.com/2011/11/how-to-calculate-production-capacity-of.html
- McLean, T. (2018, April 12). Understanding Your Production Capacity. TXM Lean Solutions. txm.com/understanding-your-production-capacity/